Additive manufacturing: which processes?
2020, August, 31
Additive manufacturing opens new avenues in geometry or materials, as new playground for professional players and also for the general public. By widening the field of possibilities, this technology also offers different processes to satisfy the greatest number.
In a non-exhaustive way, and because our article is not intended to be exhaustive, we are going to introduce you to the various processes offered by additive metal manufacturing, all with the aim of popularizing science.
The SLM process or fusion on the powder bed :
SLM stands for Selective Laser Melting. This is the process we have chosen at Precision IMS. It consists in creating a part layer by layer, by adding material. The material in the form of powder particles is fused by means of a laser beam.
The manufacturing process takes place in a chamber under neutral gas. The powder is stored in a tank, then the coating system intervenes, by depositing material (this is called a powder bed). The laser is used to melt the powder particles and gives the first section of the object. And so on, layer by layer, until the final part is obtained.
The advantages of this technique, are notable: no need for tools, valid for very complex applications, such as those with very elaborate geometries for example.
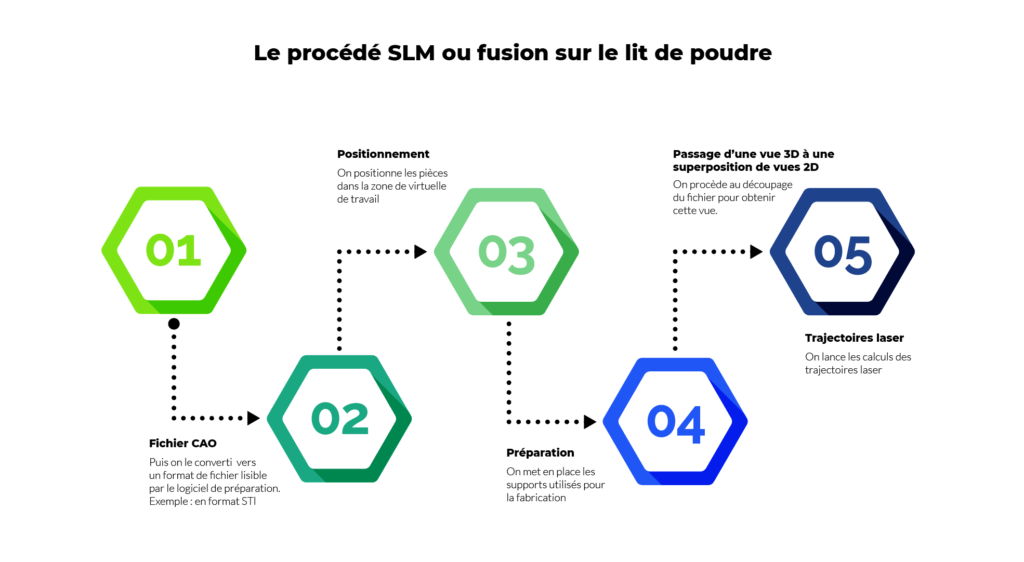
We could also talk about the DMLS (Direct Metal Laser Sintering) process, also called SLS for Selective Laser Sintering, which is very similar to the SLM process. The difference being that it is a sintering technique and not a fusion technique like SLM, and with the DMLS process there is incomplete fusion of the powder particles, whereas in SLM the powder is completely fused.
Would you like to know more about this process? Here are some contents that might interest you: a video by Matsuura and an article by All3DP.
The DED or Clad process :
DED stands for Directed Energy Deposition or Concentrated Energy Deposition. During manufacturing, focused thermal energy (usually a laser or electron beam) is used to melt the materials as they are deposited.
Today, we are even seeing the appearance of machines that incorporate recharging heads. The main advantage of this process is that it is possible to work on already existing parts and at very precise locations. Whether it is for reloading, repair, or adding functions to existing shapes, for example. You will have understood it, this process offers many possibilities to repair a part, rather than changing it for a new one, which is not negligible.
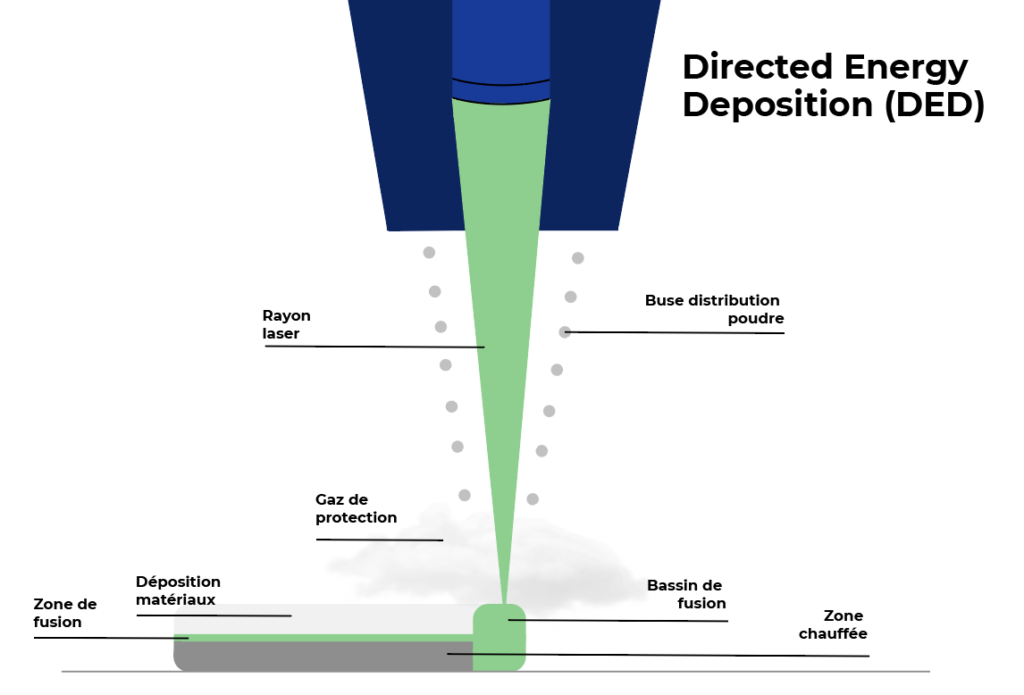
Historically, this process is related to the FDM (Fused Deposition Modeling) technique. It is the most widespread process, and certainly the best known to the general public, for example it is widely used in schools and universities. It is known to be inexpensive and easy to use.
However, the limit we could raise for this process would rather be related to the fact that the precision is not always there. It is therefore not the most efficient process for high precision applications. Moreover, to explain this, we could talk about the TRL scale: Technology Readiness Level. This is a scale for assessing the degree of maturity of a technology. It was designed by NASA to manage the technological risk of its programs. It is now widely used in cutting-edge fields such as aeronautics. If it were applied to additive manufacturing, we could say that the challenge would be to reach the highest levels as quickly as possible.
Binder Jetting :
For this process, we use a binding agent that is deposited on a thin layer of powder. Once out of the machine, there is an after-treatment step which consists in putting the part in the oven in order to solidify it. One of the advantages of this process is that it allows the creation of parts quickly and with a relatively good level of detail. So it can be chosen when creating visual prototypes for example. If we look at the materials, we can see that there are developments in the field of metal and ceramics for this process that are interesting to consider.
Also, beyond the materials available, and for applications in plastics specifically, we can obtain colored parts, by mixing the binder with compatible inks. For metal applications, this process is rather recent, promising, but with certainly less data and hindsight for industrial applications.
One of the disadvantages that we can point out for binder spraying is the fact that the mechanical properties of the parts are less resistant. So this process is not valid for all applications.