La fabrication additive : quels procédés ?
31 août 2020
La fabrication additive ouvre de nouvelles voies sur la géométrie ou les matériaux, elle ouvre un nouveau terrain de jeux pour les acteurs professionnels autant qu’aux grand public. En élargissant le champ des possibles, cette technologie propose aussi différents procédés, pour satisfaire le plus grand nombre.
De façon non exhaustive, et parce que notre article n’a pas vocation à l’être, nous allons vous introduire les différents procédés qu’offre la fabrication additive métallique, le tout avec pour objectif la vulgarisation scientifique.
Le procédé SLM ou la fusion sur le lit de poudre :
SLM signifie Selective Laser Melting. C’est le procédé pour lequel nous avons opté chez Précision IMS. Il consiste à créer une pièce couche par couche, par ajout de matière. La matière sous forme de particules de poudre se fusionne par le biais d’un faisceau laser.
Le processus de fabrication se fait dans une enceinte sous gaz neutre. On stock la poudre dans un réservoir, puis le système de mise en couche intervient, en déposant de la matière (c’est ce qu’on appelle un lit de poudre). Le laser lui, est utilisé pour la fusion des particules de poudre et donne la première section de l’objet. Et ainsi de suite, couche par couche, jusqu’à l’obtention de la pièce finale.
Les avantages de cette technique, sont notables : pas besoin d’outillages, valables pour des applications très complexes, comme celles avec des géométries très élaborées par exemple.
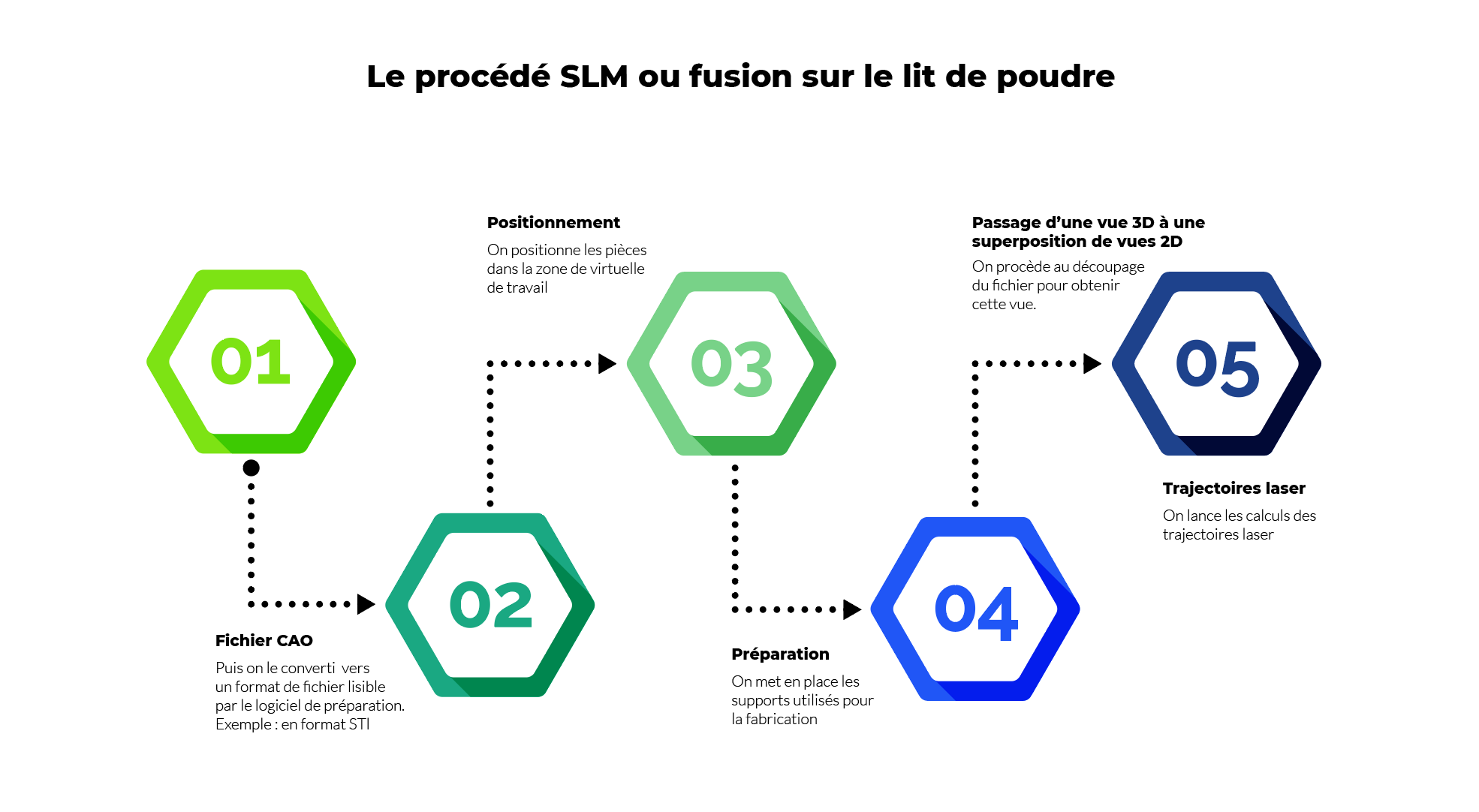
Nous pourrions aussi parler du procédé DMLS (Direct Metal Laser Sintering) aussi appelé SLS pour Selective Laser Sintering, qui se rapproche très fortement du procédé SLM. La différence étant qu’il s’agit d’une technique de frittage et non de fusion comme le SLM, et qu’avec le procédé DMLS, il y a une fusion incomplète des particules de poudres, alors qu’en SLM, la poudre est complètement fusionnée.
Vous souhaitez en savoir plus sur ce procédé ? Voici quelques contenus qui pourraient vous intéresser : une vidéo de Matsuura et un article par All3DP.
Le procédé DED ou Clad :
DED signifie Directed Energy Deposition ou dépôt sous énergie concentrée. Lors de la fabrication, une énergie thermique focalisée (généralement un faisceau laser ou faisceau d’électrons) est utilisé de façon à permettre la fusion des matériaux en les fondant au fur et à mesure qu’ils sont déposés.
Aujourd’hui, on voit même apparaitre des machines qui intègrent des têtes de rechargement. Le principal avantage de ce procédé est que l’on peut travailler sur des pièces déjà existantes et à des endroits très précis. Qu’il s’agisse de rechargement, de réparation, d’ajout de fonctions à des formes déjà existantes par exemple. Vous l’aurez compris, ce procédé offre de nombreuses possibilité pour réparer une pièce, plutôt que de la changer pour une nouvelle, ce qui n’est pas négligeable.
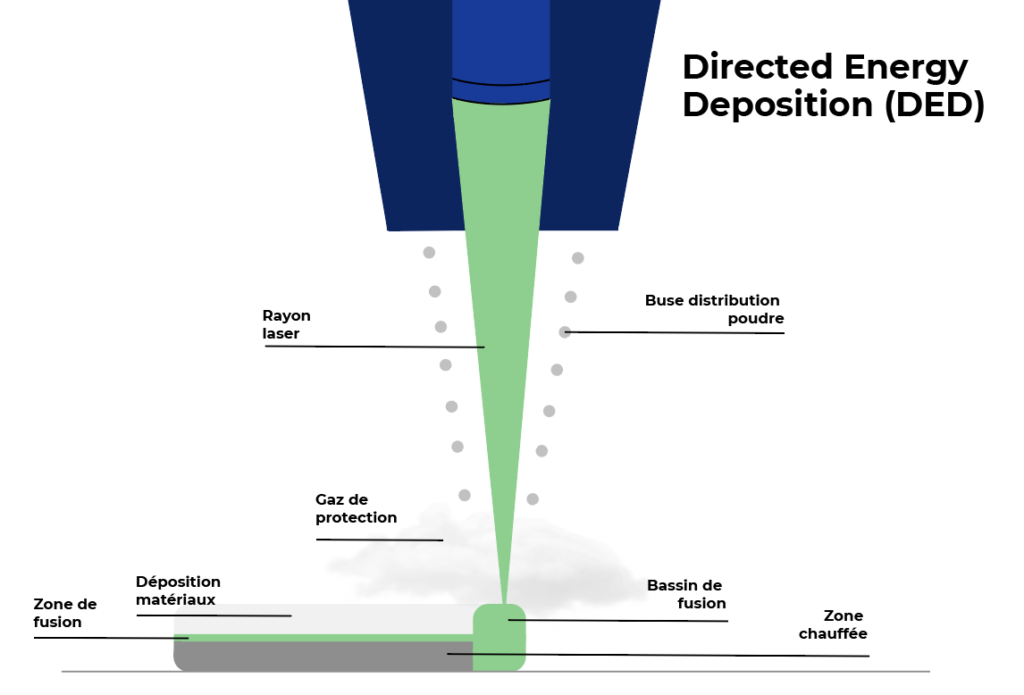
Historiquement, ce procédé a un lien de parenté avec la technique FDM (Fused Deposition Modeling), ou modélisation par dépôt de fil en fusion. C’est le procédé le plus répandu, et certainement le plus connu auprès du grand public, par exemple il est beaucoup utilisé dans les écoles et universités. Il est réputé pour être peu couteux, et facile d’utilisation.
Cependant, la limite que nous pourrions soulever pour ce procédé serait plutôt liée au fait que la précision n’est pas toujours au rendez-vous. Il ne s’agit donc pas du procédé le plus performant pour des applications de haute précision. D’ailleurs, pour l’expliquer nous pourrions parler de l’échelle TRL : Technology Readiness Level. Il s’agit d’une échelle d’évaluation du degré de maturité d’une technologie. Elle a été imaginée par la Nasa en vue de gérer le risque technologique de ses programmes. Elle est notamment aujourd’hui très utilisée dans des domaines de pointe comme l’aéronautique. Si on l’appliquait à la fabrication additive, nous pourrions dire que l’enjeu serait d’atteindre les plus hauts niveaux, le plus rapidement possible.
La projection de liant ou Binder Jetting :
Pour ce procédé, on utilise un agent liant que l’on dépose sur une fine couche de poudre. Une fois sortie de la machine, il y a une étape de post traitement qui consiste à passer la pièce au four dans le but de la solidifier. L’un des avantages de ce procédé est qu’il permet de créer des pièces rapidement et avec un relativement bon niveau de détails. On peut donc le choisir lorsque l’on crée des prototypes visuels par exemple. Si l’on se penche sur les matériaux, nous pouvons noter qu’il y a des développements dans le domaine du métal et de la céramique pour ce procédé qui sont intéressants à prendre en considération.
Aussi, au-delà des matériaux disponibles, et pour les applications dans le plastique spécifiquement, on peut obtenir des pièces en couleur, en mélangeant le liant à des encres compatibles. Pour les applications métal, ce procédé est plutôt récent, prometteur, mais avec certes moins de données et de recul pour les applications industrielles.
L’un des inconvénient que nous pouvons relever pour la projection de liant est le fait que les propriétés mécaniques des pièces sont moins résistantes. Donc ce procédé n’est pas valable pour toutes les applications.
En image, et pour exemple voici le cas HP avec la HP 3D Metal Jet